by Dan Cameron
Many articles have been written over the past several years that address changing the location of the Tiger’ s stock oil filter from the engine compartment to under the left front fender well.
Providing you are not trying to remain as near stock as possible, moving the oil filter out-board has at least two advantages: Ease of changing the filter due to the spin-on feature. It is one more item removed from the engine compartment providing the potential for increased air flow.
I recently went through this procedure and am very pleased with the results; however, many times along the way I felt like throwing in the towel. What made the job so difficult was finding a satisfactory block-off plate (adapts to block) that would clear my headers. This is not a problem with the stock exhaust system or with the headers that go over the top of the engine mount. If you have either of the latter two conditions, you can use Rapid Cool’s (Hayden Inc., Corona, CA) block-off plate #103271-01. As opposed to other makes, it was designed to port straight out of the block (90 degrees to crank) or port to the side (parallel to crank toward front of car). I thought the block-off plate with side porting would solve my clearance problem with the headers.
So I went ahead and ordered it along with the remote oil filter mount itself, #1021040-01. The filter mount, by the way works great. No such luck with the block-off plate. Significant persuasion with the old hammer on the old headers was going to be required to get it to fit. After many hours of deliberation, I finally concluded there just was not an adapter manufactured that would do all I wanted it to do: clear headers and frame adapt to 0.500″ I.D. Stainless braided hose look professional.
The solution to the problem: use stock Tiger block adapter and fabricate hose end fittings to interface with braided hose. It sounds simple, but the Tiger’s block adapter requires 0.500″, inverted flare, and male fittings. These are the same as on the original hoses which can be cut off and used.
If you elect not to butcher your old hoses, you are in for a treat. The 0.500″ inverted flare nuts must have been a one-time build in merry old England. Most of my parts suppliers said they had “just what I wanted” -wrong !! When the stock was pulled from the shelf, 0.375″ was about the largest available. The material required to fabricate the hoses is as follows:
- (2) 0.500″ inverted flare male nuts.
- (2) hose adapter fittings (fit into 0.500″ I.D. hose). These are conical with a corrugated O.D. Gates manufactured the ones I used. They are available at most hydraulic hose repair shops.
- (2) ten inch long pieces of 0.500″ I.D. x 0.049″ wall seamless tubing
- Fifty-one inch length of 0.500″ I.D. teflon lined, braided hose
- The stock block-off plate and remote oil filter mount mentioned earlier
The first step in constructing the oil lines is to fabricate the hose end fittings. The tubular portion that mates to the block-off plate will be a different length (shorter) for the incoming oil line as compared to the oil line going to the filter. The sketch provided should get you started in the right direction.
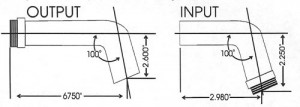
Remember, “two things that aren’t the same are different” this applies to Tigers as well. Double check length and angle of bend with coat hanger wire on your particular car before going too far. Note that in each case the angles (100 degrees included), and radii of bend (0.750″) are the same. I purchased my tubing from an industrial supply house that manufactures hydraulic lines and had them do the bending. Standard tube bending equipment limits the tightness of the radius before collapsing the tube. They can also put a double flare on the tube end that will guarantee a positive seal.
The second step is to take the two steel lines with flared nuts to your local welding shop to have the hose fittings brazed or silver soldered to the end opposite the flare nuts. The latter is really the preferred method for seal and appearance. With the completion of die hose end fittings, I took them to an automotive parts house that specializes in making up air conditioning hoses, oil lines, etc. Using two different length hoses, 25.5 ” for the line going to the filter and 26.5″ for the line returning from the filter, I had them swage (crimp) the braided lines to my hose end fittings. Again, be sure to check the measurements for your specific application.
Now, for that added professional touch, paint the hose end fittings with Zynatyte Super Chrome Epoxy Paint prior to installation.
Finally, to install the completed lines, cut two 0. 875″ holes in the left hand side of the engine compartment sheet metal that will access the inside of the fender well. I drilled (rotary saw) holes 5.375″ and 7.125″ back from the radiator bulkhead, just in front of the leading edge of the header coolant tank.
Next, place 0.625″ I.D. rubber grommets over the two hose lines and you are ready to install the lines in the car. Start with the line supplying oil to the filter. Coat the threads with teflon liquid seal or tape and screw the inverted flared nut to the block adapter. This will route the line forward and above the steering column link. The second line, which which brings oil from the filter and into the center of the block adapter, is routed under the column steering link, then runs parallel to the first line to the remote oil filter.
Next, secure lines to remote filter. Position them under the fender as close to the headlight bucket as possible.
Mark this location, drill mounting holes and bolt in place. I know it sounds like a lot of work, but it’s not so bad once you get started. Good luck!